Vacuum Release Tray
2024.05.23 / By admin
Meta Descriptions
CrysPack offers vacuum release tray for efficient packaging solutions. Ensure secure transport and storage with our high-quality trays.
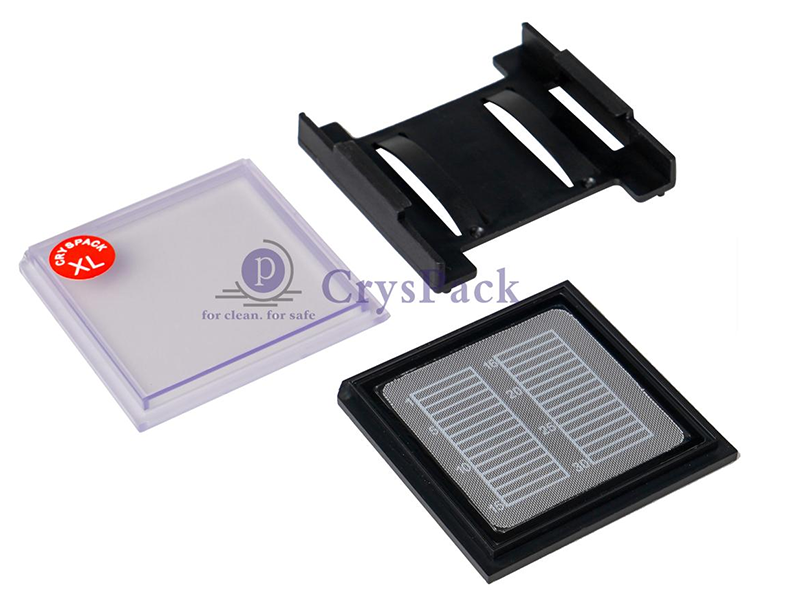
Selecting Vacuum Release Tray: Choosing Confidence, Choosing Control
In the realm of semiconductor manufacturing and handling, delicacy is paramount. With the advent of CrysPack’s Vacuum Release™ (VR) Trays, a new era of secure and damage-free handling has emerged. These trays, crafted with precision and innovation, offer a comprehensive solution to the challenges posed by fragile components such as bare die. Let’s delve deeper into the features, applications, and configurations of these cutting-edge trays.
Unveiling the Technology Behind VR Trays
At the heart of CrysPack’s VR Trays lies a proprietary technology that sets them apart from conventional solutions. These trays employ a unique Gel or non-silicone Vertec™ film membrane, strategically placed over a mesh material. This combination ensures the secure confinement of delicate components, such as bare die, while they undergo various stages of shipping, handling, and processing.
1. Gel and Vertec™ Film Membranes: The Gel and Vertec™ film membranes serve as the backbone of VR Trays, providing unparalleled adhesion and protection to fragile devices. Their flexibility and resilience make them ideal for accommodating devices ranging from <250 microns to 75mm in size.
2. Pocketless Design: One of the standout features of VR Trays is their pocketless design, which eliminates contact with the edges or the top surface of the device. This meticulous design approach minimizes the risk of damage during handling, ensuring the integrity of the components.
3. High-Volume Automation Compatibility: In the realm of high-volume manufacturing, efficiency is key. VR Trays are engineered to seamlessly integrate into automated pick and place applications, facilitating swift and precise handling of delicate components without compromising on quality.
Exploring the Versatility of VR Trays
The versatility of VR Trays extends beyond their innovative design. From handling fragile devices to catering to diverse application requirements, these trays offer a myriad of benefits.
1. Handling Fragile or Thin Devices: Whether it’s delicate semiconductor components or ultra-thin devices, VR Trays provide a secure and stable platform for handling. Their ability to safeguard fragile devices throughout the shipping, handling, and processing stages ensures peace of mind for manufacturers.
2. Securely Holding Bare Die: Bare die, devoid of packaging, poses a unique set of challenges in terms of handling and protection. VR Trays address this challenge head-on by securely holding bare die in place, minimizing the risk of damage or contamination.
3. Ideal for High-Volume Automated Applications: With the advent of automation in manufacturing, VR Trays prove to be indispensable. Their compatibility with high-volume pick-and-place applications streamlines the production process, enhancing efficiency and productivity.
Diving into VR Tray Configurations
CrysPack’s commitment to customization and flexibility is reflected in the diverse configurations offered for VR Trays. From tack levels to tray sizes, manufacturers have the freedom to tailor these trays to their specific requirements.
1. Tack Levels: VR Trays are available in a spectrum of tack levels, catering to a wide range of application requirements. Whether it’s minimal adhesion for delicate components or stronger adherence for secure handling, manufacturers can choose the tack level that best suits their needs.
2. Tray Sizes: Based on JEDEC standards, VR Trays are offered in 2” and 4” sizes, providing manufacturers with options to accommodate various device dimensions and production setups.
3. Membrane Options: Manufacturers can choose between Gel or Vertec™ film membranes based on their preferences and application requirements. Each membrane offers distinct advantages in terms of adhesion, flexibility, and compatibility.
4. Variety of Tray/Lid Combinations: To further enhance customization, VR Trays are available in transparent, conductive black, and transparent antistatic options. Additionally, customization options such as printing or grid patterns allow manufacturers to tailor these trays to their branding or operational needs.
Choosing the Correct VR Tray
1. Mesh Size Matters: Tailoring VR Trays to Device Dimensions
When it comes to selecting the appropriate VR tray, mesh size plays a crucial role. CrysPack offers a range of mesh geometries, including 16, 33, 76, 103, 137, and 195, meticulously designed to optimize offloading performance. The mesh size should align with the X and Y dimensions of the device, ensuring optimal support and stability during transportation and storage.
2. Customizable Tack Level: Adapting Holding Force to User Requirements
CrysPack’s VR trays feature Gel or Vertec film membranes with varying tack levels, ranging from ultra-low to high. This customization empowers users to adjust the holding force according to their specific needs. Whether securing delicate microchips or larger electronic components, selecting the appropriate tack level ensures reliable adhesion without compromising ease of removal.
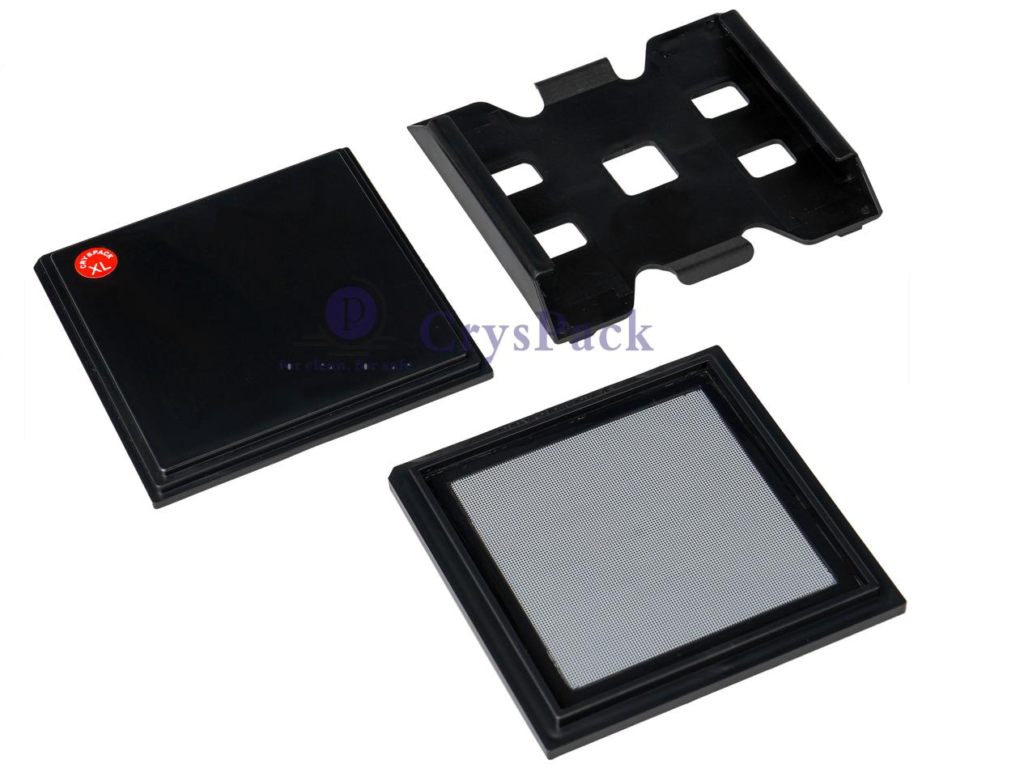
How VR Technology Works
1. Hold Mode: Ensuring Secure Device Encapsulation
In hold mode, VR trays firmly secure devices in place for shipping, handling, and storage. The Gel membrane establishes maximum surface contact with the device, minimizing the risk of movement or damage during transit. This robust hold mode provides reassurance to manufacturers and distributors, safeguarding valuable electronic components throughout the supply chain.
2. Release Mode: Facilitating Effortless Device Retrieval
The beauty of VR technology lies in its seamless transition to release mode. By applying a vacuum through a strategically positioned hole in the underside of the tray, surface contact between the Gel membrane and the device is minimized. This reduction in holding force enables easy device removal using a vacuum pick-up tool, streamlining operational processes and minimizing handling time.
3. Reusable Design: Sustainability Meets Practicality
CrysPack’s VR trays boast a reusable design, embodying sustainability and cost-effectiveness. The hold and release process can be repeated multiple times on the same tray without compromising performance or integrity. This durability not only reduces environmental impact but also enhances operational efficiency, making VR trays a smart investment for businesses striving for excellence.
Usage Tips for Optimal Performance
1. Minimize Downforce: Preserving Device Integrity
During device unloading, it’s imperative to minimize the pick-up tool’s overdrive to prevent potential damage. Excessive downforce can exert undue pressure on delicate components, compromising their integrity and functionality. By exercising caution and precision, users can safeguard devices while maximizing efficiency.
2. Avoid Tweezers: Opting for Safe Handling Practices
While tweezers may seem like a convenient tool for device retrieval, they pose a risk of puncturing the Gel membrane if used incorrectly. To mitigate this risk, it’s advisable to refrain from using tweezers and instead opt for vacuum pick-up tools specifically designed for VR tray applications. This proactive approach minimizes the likelihood of damage and ensures smooth operations.
3. Optimize Mesh Size and Tack Level: Fine-Tuning Performance Parameters
To achieve optimal results, users should carefully consider both mesh size and tack level when selecting VR trays. By aligning these parameters with the device’s specifications, unload force requirements can be minimized, enhancing operational efficiency and device protection. CrysPack’s comprehensive range of options facilitates customization tailored to individual needs, ensuring unparalleled performance across diverse applications.
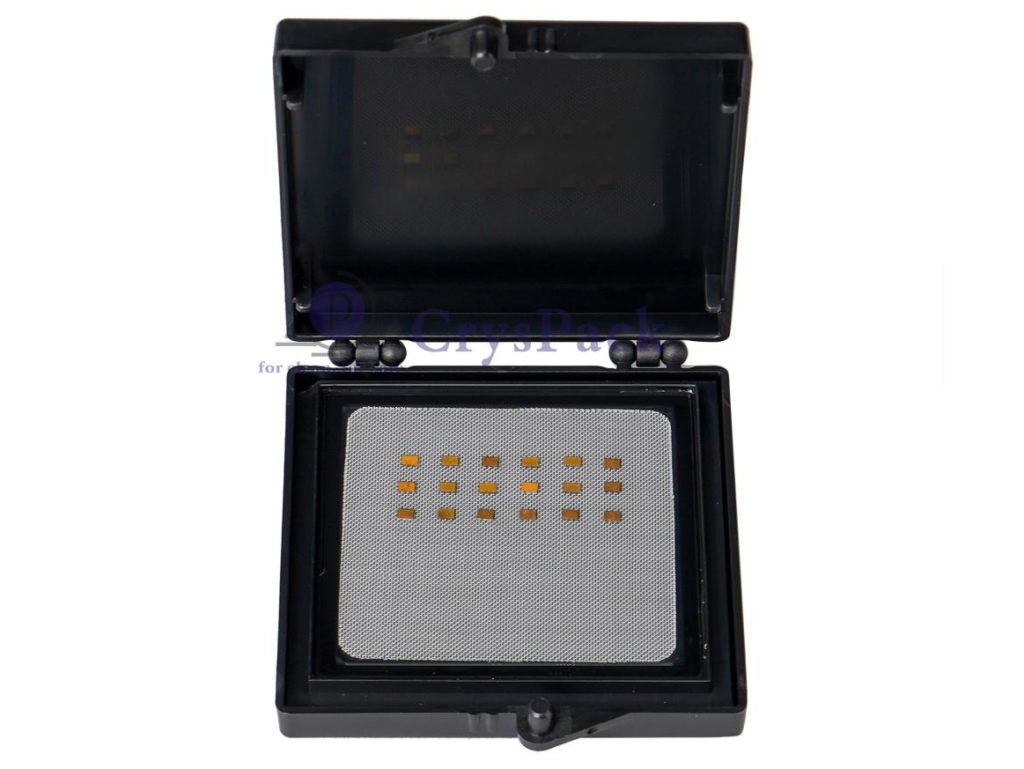
Conclusion: Elevating Device Handling Standards with VR Trays
CrysPack’s Vacuum Release™ (VR) Trays represent a paradigm shift in the realm of delicate device handling. With their innovative design, versatility, and customization options, these trays offer a comprehensive solution to the challenges posed by fragile components. As semiconductor manufacturing continues to evolve, VR Trays stand poised to elevate handling standards and redefine industry norms.
For manufacturers seeking to safeguard their delicate devices and optimize production efficiency, CrysPack’s VR Trays emerge as the go-to choice, ensuring secure and damage-free handling every step of the way.