Why Industries Rely on Vacuum Release Box: Optimizing Operations
2024.07.08 / By hqt
In industrial and electronic sectors where secure equipment fixation and easy removal are paramount, the Vacuum Release Box (Vacuum Release Box) stands out as a crucial innovation. This specialized device, pioneered by Cryspack, facilitates the secure attachment and swift detachment of equipment during transportation and operational phases. By manipulating the contact area of an elastic film within the tray, the Vacuum Release Box effectively alters adhesive forces, ensuring firm fixation when required and effortless removal when needed.
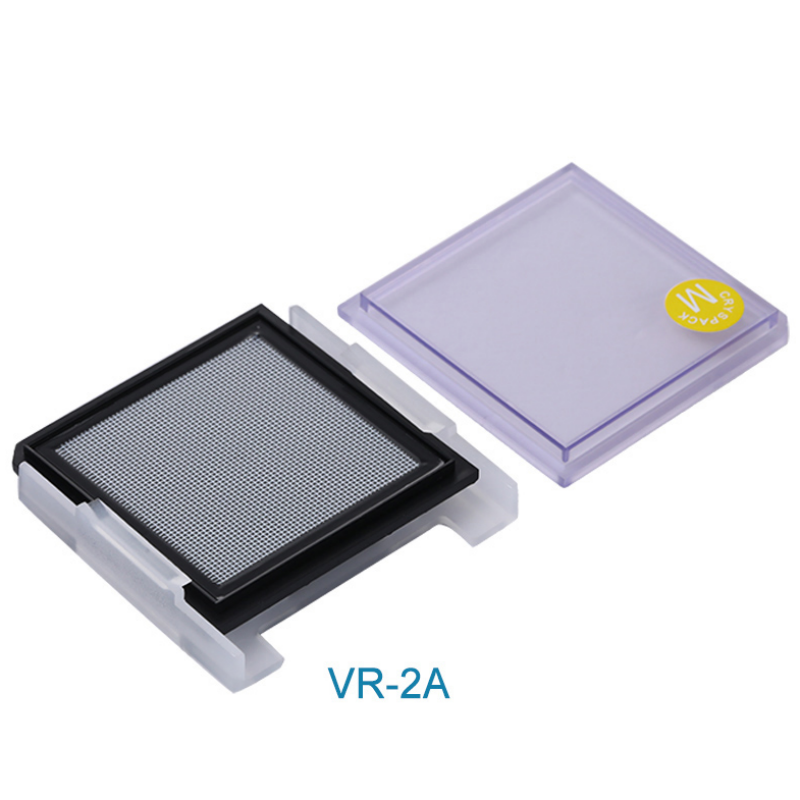
What is Vacuum Release Box: A Versatile Solution
The Vacuum Release Box (Vacuum Release Box) is a specialized device designed to securely hold and release delicate equipment during transportation, installation, and operational phases. This innovative technology, pioneered by Cryspack, leverages the manipulation of surface contact through an elastic film within the tray. By adjusting the contact area, the Vacuum Release Box can either firmly fix equipment in place or facilitate easy removal when required, making it an indispensable tool across various industries.
Applications in Semiconductor Industry
In the semiconductor industry, where precision and reliability are paramount, the Vacuum Release Box plays a crucial role in handling sensitive components and equipment. Semiconductor fabrication processes involve the use of intricate machinery and delicate materials that require careful handling to prevent damage and ensure operational efficiency. Vacuum Release Boxes from Cryspack offer customizable configurations and retention levels, providing secure attachment while enabling seamless removal during critical manufacturing stages. This capability not only enhances production efficiency but also minimizes the risk of equipment damage, contributing to overall yield improvement and cost-effectiveness in semiconductor manufacturing.
Semiconductor manufacturers benefit from Cryspack’s Vacuum Release Boxes by integrating them into cleanroom environments where adherence to stringent contamination control protocols is essential. The ability to securely hold equipment without leaving residues or marks simplifies maintenance and ensures cleanroom integrity. Moreover, the Vacuum Release Box’s compatibility with JEDEC standards ensures seamless integration with existing semiconductor equipment trays, facilitating streamlined workflows and reducing operational complexities.
Opto-Electronics Industry Utilization
In the opto-electronics industry, which encompasses the production of optical devices, sensors, and display technologies, the Vacuum Release Box serves as a reliable solution for securely transporting and handling delicate optical components. Opto-electronic devices often require precise alignment and minimal disturbance during assembly and testing phases to maintain performance integrity. Cryspack’s Vacuum Release Boxes offer various mesh geometries and retention levels tailored to accommodate different sizes and weights of optical components, ensuring stable fixation during transportation and assembly processes.
The optical clarity of the Vacuum Release Box’s elastic film ensures that optical components are held securely without compromising light transmission or optical performance. This feature is critical in applications such as laser optics, where any deviation in alignment or surface contamination can significantly affect device functionality. By providing a clean and secure environment for handling optical components, Cryspack’s Vacuum Release Boxes contribute to improving production yield and maintaining high standards of optical device performance and reliability.
Telecommunication Industry Integration
In the telecommunication industry, the Vacuum Release Box serves as a versatile tool for handling and transporting sensitive electronic modules and components used in telecommunications infrastructure. Telecommunication equipment, such as RF modules, transceivers, and network processors, requires secure fixation during installation and maintenance to ensure optimal performance and reliability of communication networks. Cryspack’s Vacuum Release Boxes, with their customizable configurations and anti-static properties, provide an ideal solution for securely holding and releasing telecom components without causing electrostatic discharge (ESD) or mechanical damage.
Telecommunication operators and equipment manufacturers benefit from the Vacuum Release Box’s ability to streamline installation and maintenance procedures, thereby reducing downtime and enhancing operational efficiency. By minimizing the risk of damage during handling and transportation, Cryspack’s Vacuum Release Boxes contribute to extending the lifespan of telecommunication equipment and improving overall network reliability. The compatibility of Vacuum Release Boxes with standardized tray sizes and retention levels ensures interoperability with various telecommunications equipment, supporting industry-standard practices and operational workflows.
Understanding the Market Dynamics and Needs
The market demand for reliable equipment fixation solutions is on the rise across various industries. Manufacturers and operators seek methods that balance secure attachment with ease of handling to optimize efficiency and reduce operational downtime. Traditional methods often fall short, either providing insufficient security or complicating equipment removal, thus necessitating a solution like the Vacuum Release Box.
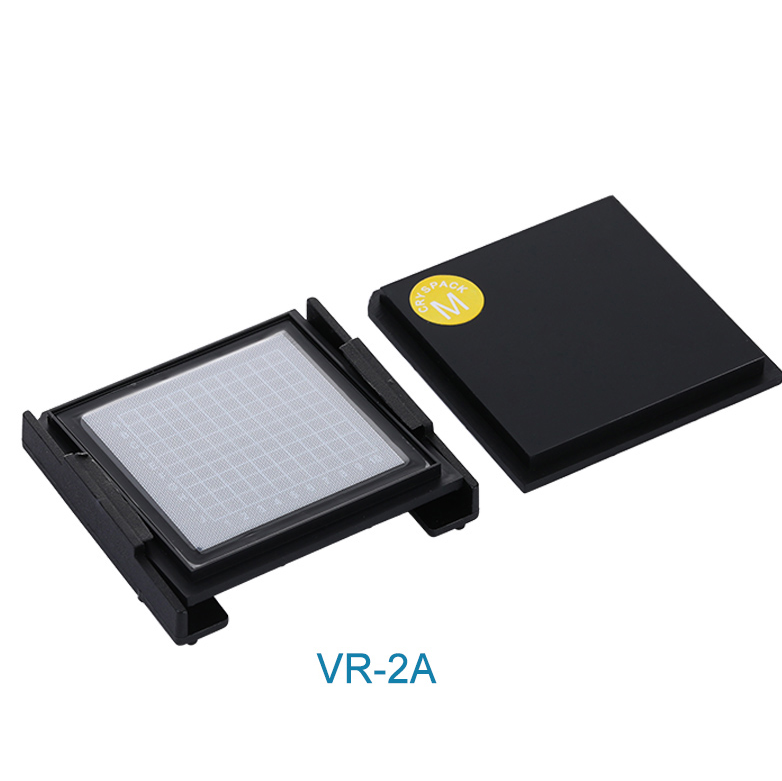
In sectors such as semiconductor manufacturing, aerospace, and automotive industries, where delicate and expensive equipment must be transported and installed securely, the Vacuum Release Box fills a critical gap. Its ability to adjust adhesion levels ensures that equipment remains stable during transit and operation, mitigating risks of damage or misalignment.
Cryspack’s Vacuum Release Box: Meeting Industry Needs with Precision
Cryspack has emerged as a leader in the development and production of Vacuum Release Boxes, offering a range of configurations tailored to meet specific industry requirements. Their Vacuum Release Boxes are designed according to JEDEC standards, featuring tray sizes ranging from 2 inches to 6 inches, accommodating various equipment dimensions commonly used in industry standards.
Configurations and Specifications
Cryspack’s Vacuum Release Boxes come equipped with a diverse array of features designed to optimize functionality and adaptability:
Tray Sizes and Standards: Available in 2-inch, 4-inch, 5-inch, and 6-inch configurations, adhering to JEDEC standards, ensuring compatibility with a wide range of equipment.
Retention Levels: Offered in XL, L, M, H, and HH levels of retention, providing flexibility to adjust adhesive forces based on equipment weight and environmental conditions.
Mesh Geometries: Various mesh sizes (16, 33, 76, 103, 137, and 195) allow customization of contact area, optimizing adherence while facilitating easy equipment removal.
Customization Options: Print patterns on the elastic film can be customized to meet specific customer branding or identification needs, enhancing traceability and organizational efficiency.
Innovative Technology Behind the Vacuum Release Box
At the heart of Cryspack’s Vacuum Release Box technology lies the innovative manipulation of the contact area of the elastic film. During storage and operation, the film maximizes surface contact, firmly securing the equipment in place. When removal is required, applying vacuum through the tray’s bottom hole causes the film to conform to mesh patterns, minimizing surface contact points and thereby reducing adhesion force. This simple yet effective mechanism ensures that equipment can be lifted out effortlessly, avoiding potential damage or operational delays.
Market Adoption and Future Prospects
Since its introduction, Cryspack’s Vacuum Release Box has garnered significant attention and adoption across industries where equipment security and operational efficiency are critical. Semiconductor manufacturers, for instance, have integrated Vacuum Release Boxes into their processes to streamline equipment handling during fabrication and assembly stages. Aerospace companies also benefit from the Vacuum Release Box’s ability to securely transport sensitive components without compromising on safety or efficiency.
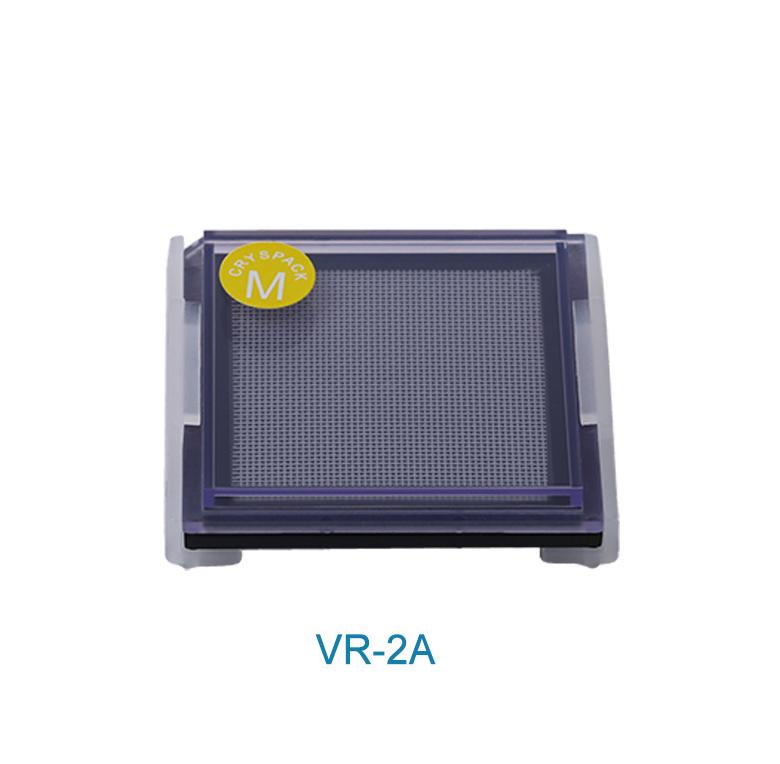
Looking forward, Cryspack continues to innovate, exploring new materials and technologies to enhance Vacuum Release Box performance and expand its applicability across diverse industrial sectors. By addressing specific pain points in equipment handling and transport, Cryspack remains committed to driving efficiency and reliability in manufacturing and operational workflows worldwide.
Conclusion
The Vacuum Release Box from Cryspack represents a significant advancement in equipment handling technology, providing a robust solution for secure attachment and easy removal. With its customizable configurations, innovative design, and widespread market adoption, the Vacuum Release Box is poised to revolutionize how industries approach equipment fixation and handling challenges. As industrial demands evolve, Cryspack remains at the forefront, continually refining and expanding the capabilities of the Vacuum Release Box to meet the ever-changing needs of its global clientele.