Best Vacuum Release Tray for Fragile Device Handling
2024.10.31 / By hqt
In industries where precision and fragility meet, ensuring the safe handling, transport, and storage of sensitive components is a paramount concern. Enter the vacuum release tray, an innovative solution designed to safeguard delicate devices like bare die during high-volume operations. But what exactly makes this tray such a game-changer for industries such as semiconductors, medical devices, and aerospace manufacturing? Let’s dive deeper into this remarkable technology and explore how it’s transforming device handling for the better.
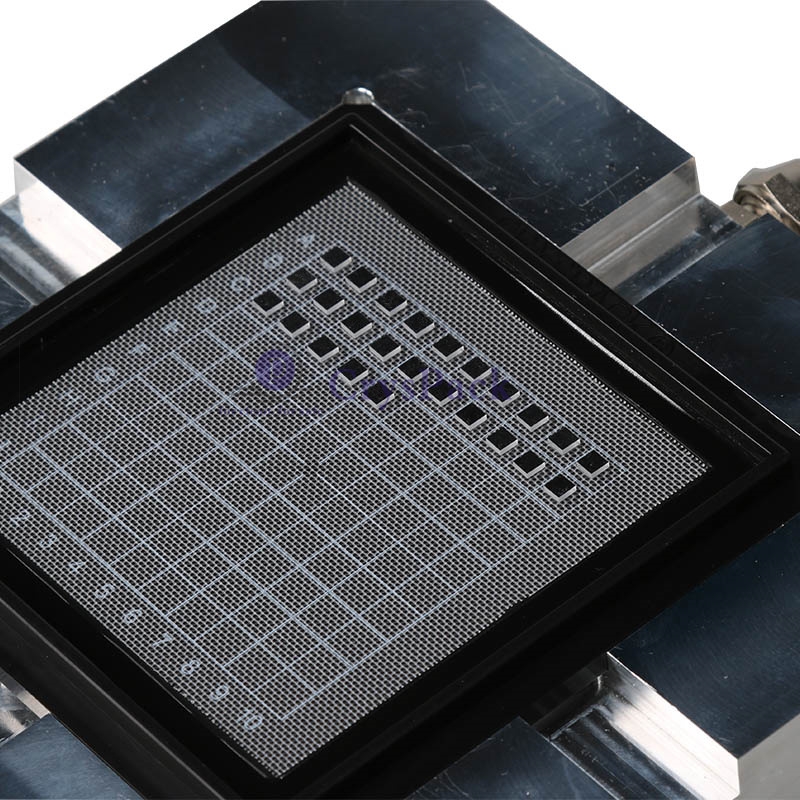
What is a Vacuum Release Tray?
A Revolutionary Tool for Delicate Components
At the heart of the vacuum release tray lies its ability to securely hold fragile devices during shipping, handling, and processing, making it ideal for high-volume, automated pick-and-place applications. What sets the vacuum release tray apart from traditional packaging solutions is its innovative design: instead of relying on pockets to hold devices, it uses a unique membrane—made from proprietary Gel or non-silicone Vertec™ film—over a mesh surface. This membrane gently grips the components, ensuring no direct contact with their edges or top surfaces, which are often vulnerable to damage.
The Science Behind the Tray
The magic of the vacuum release tray lies in its “vacuum release” mechanism. When a vacuum is applied to the underside of the tray, it releases the devices, allowing them to be effortlessly picked up or placed by automation systems. This feature is particularly valuable in environments where speed and precision are essential. To further illustrate this, Cryspack—a leading supplier of vacuum release trays—provides detailed guides and illustrations to demonstrate how this technology works.
Ideal Applications for the Vacuum Release Tray
The vacuum release tray shines in scenarios where the handling of fragile or extremely thin devices is necessary. These devices may range in size from under 250 microns to 75mm in diameter, and the tray ensures their safe handling without compromising their integrity. Industries that rely on high-volume automated device pick-and-place applications, such as semiconductor manufacturing, medical devices, and automotive production, can all benefit from the precision and care the vacuum release tray offers.
Why Choose Cryspack for Vacuum Release Trays?
A Trusted Supplier with a Global Reach
When it comes to sourcing vacuum release trays, Cryspack stands out as a global leader in precision packaging solutions. Founded in 2005, Cryspack has earned a reputation for innovation, quality, and customer service, with over 1,000 active customers around the world. The company’s dedication to “Today’s quality, tomorrow’s market” reflects its commitment to providing reliable products that meet the most stringent industry standards.
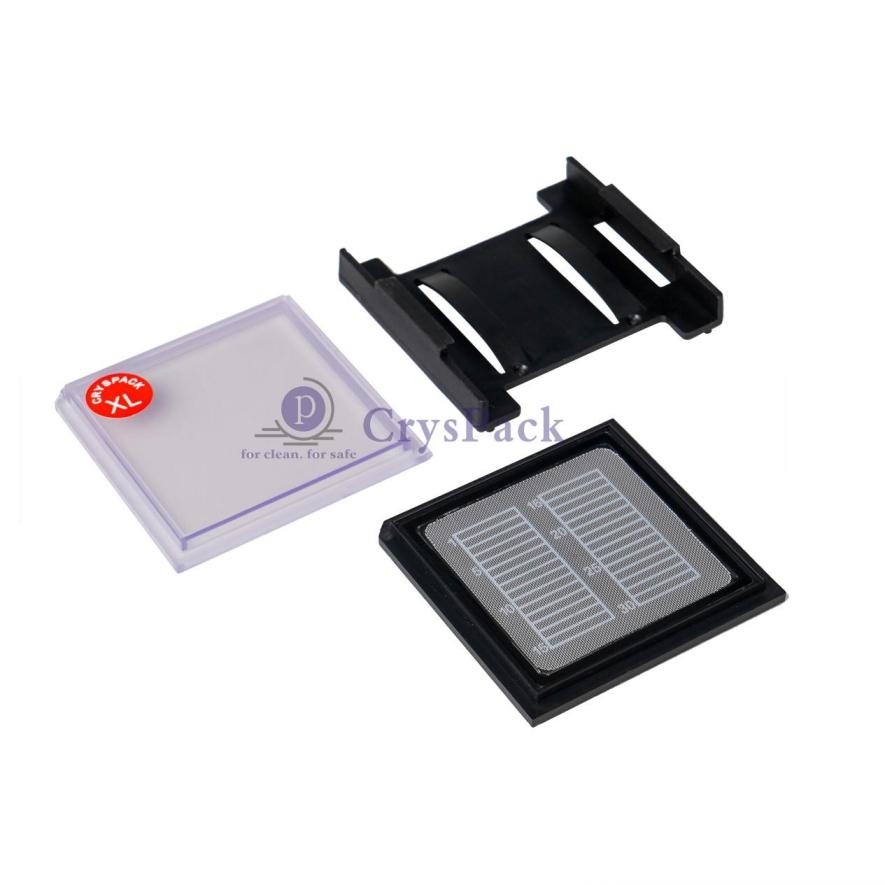
Customization Options for Every Need
Cryspack’s vacuum release trays come in various configurations, ensuring they can be tailored to meet the specific needs of different industries. Whether it’s the tack level of the membrane, the mesh size, or the overall tray configuration, customers can choose from a wide range of options to optimize performance for their particular use case. Cryspack even offers customizable print or grid patterns for added convenience. For devices smaller than 250 microns, Cryspack recommends using its NDT tray, while devices larger than 75mm can be safely accommodated in Wafer or Large Format VR plates.
Meeting Industry Standards and Beyond
Cryspack’s products aren’t just innovative—they’re also safe and reliable. All Cryspack products, including vacuum release trays, comply with EU ROHS and REACH certification standards, ensuring they are free from harmful substances and suitable for use in a wide variety of industries. These include semiconductors, optoelectronics, microwave technology, telecommunications, medical devices, automotive production, and more.
The Advantages of Vacuum Release Trays Across Industries
Semiconductor Manufacturing
In the semiconductor industry, the precise handling of delicate wafers and bare die is crucial. The vacuum release tray offers a secure way to store and transport these components without subjecting them to the risk of physical damage. Its non-contact handling capability ensures that the device’s sensitive surfaces remain pristine, while its compatibility with high-volume pick-and-place automation makes it a perfect fit for semiconductor manufacturing processes.
Medical Device Applications
For medical devices, cleanliness and sterility are of utmost importance. Vacuum release trays designed for medical use are often built to maintain sterile conditions, ensuring that fragile trays used in cleanrooms remain free of contaminants. The Gel or Vertec film membrane used in these trays provides excellent holding power without introducing foreign materials, making them an ideal choice for handling sensitive medical components.
Aerospace and Automotive Uses
The aerospace and automotive industries rely on precision-engineered components that need to be transported and stored with care. The vacuum release tray is a go-to solution for protecting vacuum trays used in aircraft manufacture and automotive part production. Its ability to safeguard devices without any direct contact to vulnerable surfaces makes it an indispensable tool for these industries.
Optimizing Vacuum Release Trays: Tack Level, Mesh Size, and More
Choosing the Correct Mesh Size
One of the key decisions when selecting a vacuum release tray is choosing the right mesh size. Mesh size determines how the membrane holds the device, and Cryspack offers a range of geometries (16, 33, 76, 103, 137, and 195) to accommodate devices of different X and Y dimensions. Proper mesh selection ensures optimal offloading performance, so it’s critical to choose the right size based on the device’s specific requirements.
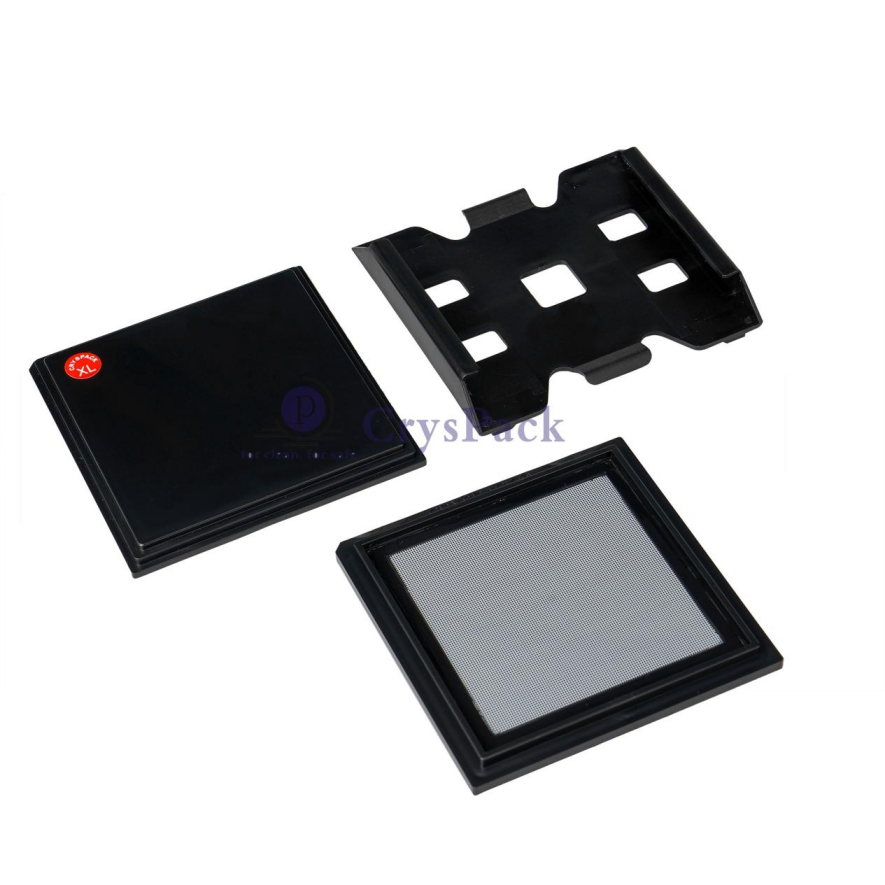
Tack Level Variations
The tack level of the Gel or Vertec film membrane can be customized to meet the needs of different devices. Ranging from ultra-low to high tack levels, Cryspack offers various options to suit different applications. Devices that are particularly fragile or lightweight might benefit from higher tack levels, while sturdier devices may only require a lower tack membrane.
Tray Configurations and Customization
Cryspack’s vacuum release trays are available in a wide variety of configurations to meet the demands of different industries and environments. Customers can choose between 2” and 4” tray sizes, based on JEDEC standards, and can opt for different lid or hinged box combinations. These options include transparent, conductive black, and transparent antistatic materials, making it easy to find a solution that suits the exact needs of a given application. For further customization, Cryspack offers the ability to add prints or grids to the trays, enhancing their functionality.
The Role of Cryspack in Vacuum Release Tray Innovation
Leading the Way in Precision Packaging
As a company that prides itself on innovation, Cryspack has continuously pushed the boundaries of what’s possible in precision packaging. Their development of vacuum release trays, membrane boxes, and other cutting-edge packaging solutions has helped countless companies in high-tech industries improve the safety and efficiency of their operations.
A Global Network of Satisfied Customers
With over 1,000 customers worldwide, Cryspack has established itself as a trusted partner for companies seeking high-quality packaging solutions such as membrane boxes, gel sticky boxes, vacuum release trays, and vacuum release boxes. The company’s reach extends across multiple industries, from semiconductors to telecommunications to automotive production, and its products are relied upon for their durability, reliability, and customizability.
Commitment to Quality and Customer Satisfaction
Cryspack’s commitment to quality is evident not only in the materials they use but also in their approach to customer service. The company’s dedication to providing innovative solutions, fast-response support, and custom services ensures that every customer has a positive experience. Whether it’s customizing a vacuum release tray for a specific application or providing expert guidance on product selection, Cryspack goes above and beyond to meet its customers’ needs.
Conclusion: The Future of Fragile Device Handling
In today’s fast-paced technological landscape, the need for precise, reliable handling of delicate components has never been greater. Vacuum release trays, especially those from industry leader Cryspack, provide a solution that meets this demand while offering versatility, customization, and superior protection. Whether you’re in semiconductor manufacturing, medical devices, aerospace, or automotive production, these trays ensure that your fragile devices are handled with care and precision every step of the way.