Exploring the Versatility of Vacuum Release Trays by Cryspack
2024.07.12 / By hqt
Vacuum release trays by Cryspack are designed to meet the diverse needs of handling delicate electronic components with utmost care and efficiency. They offer a range of customizable options that cater to specific requirements in various industrial applications.
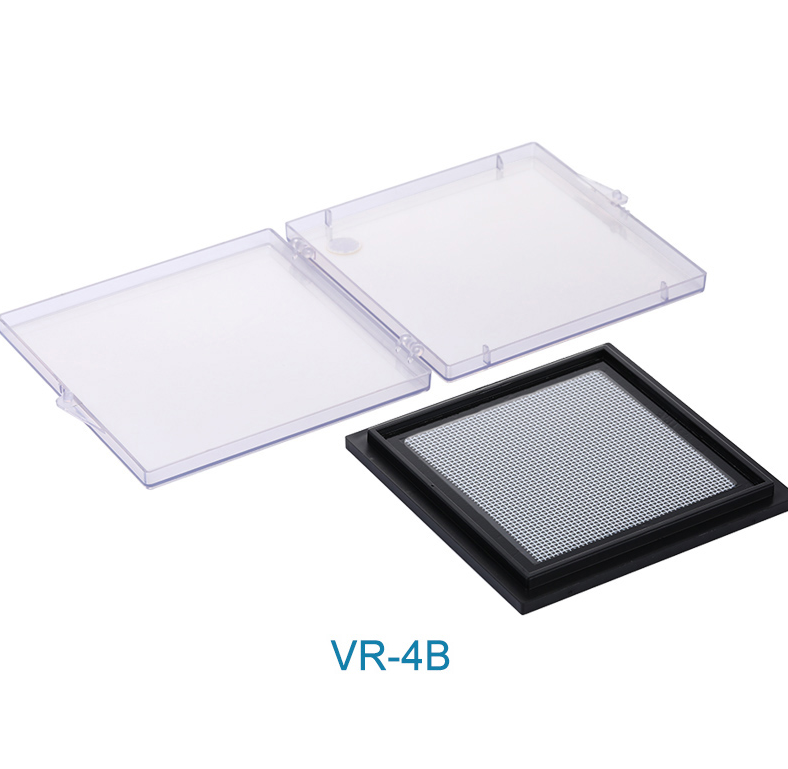
Introducing the Vacuum Release Tray
The vacuum release tray, pioneered by Cryspack, stands as a pinnacle of innovation in handling delicate electronic components. Designed to securely hold fragile devices such as bare die during shipping, handling, and processing, this “pocketless” tray employs advanced materials and technology to ensure utmost protection and ease of use.
Cryspack’s vacuum release tray utilizes a proprietary Gel or non-silicone Vertec™ film membrane layered over a mesh material. This combination effectively grips components in place until released by applying vacuum to the tray’s underside. This mechanism allows for secure handling without direct contact with the device’s edges or top surface, crucial for maintaining the integrity of sensitive components.
Understanding VR Technology
The technology behind Cryspack’s VR tray is both sophisticated and reliable. By leveraging Gel or Vertec™ film membranes with varying tack levels, the tray accommodates a wide spectrum of device sizes, ranging from less than 250 microns to 75mm in dimension. This flexibility makes it ideal for high-volume automated pick and place applications, where precision and efficiency are paramount.
The VR tray’s configuration options are extensive, offering choices between 2” and 4” tray sizes based on JEDEC standards. Furthermore, Cryspack provides customization options such as transparent, conductive black, and transparent antistatic trays. These trays can also be tailored with prints or grids to meet specific customer needs, ensuring compatibility with diverse manufacturing environments.
Applications of Vacuum Release Tray
Handling Fragile Devices
One of the primary applications of Cryspack’s vacuum release tray is in handling extremely fragile or thin devices. Whether it’s delicate microelectronics or bare die, the tray’s gentle yet secure grip ensures that components remain intact and undamaged throughout their journey from production to assembly.
Automated Pick & Place
In high-volume manufacturing environments, efficiency is key. The VR tray excels in automated pick and place operations, offering a reliable means to transport and position components without manual intervention. This capability not only speeds up production processes but also reduces the risk of human error, enhancing overall yield and consistency.
Versatility in Device Size Handling
From minuscule components measuring less than 250 microns to larger devices up to 75mm in size, Cryspack’s VR tray adapts effortlessly to various dimensions. This adaptability is critical for industries where different device sizes are common, providing a single solution that can accommodate a range of product specifications.
Choosing the Right VR Tray
Mesh Size Selection
Choosing the right mesh size is crucial in optimizing the performance of Cryspack’s vacuum release trays. The available mesh sizes include 16, 33, 76, 103, 137, and 195, each tailored to accommodate different dimensions of electronic components. A finer mesh size, such as 16 or 33, is suitable for smaller devices, providing a tighter grip that prevents movement during handling and transport. On the other hand, larger mesh sizes like 137 or 195 are ideal for larger components, ensuring secure placement while allowing efficient release when required.
The mesh size selection process involves assessing the dimensions of the components that will be housed in the tray. Cryspack’s comprehensive range ensures that manufacturers can find an optimal solution that balances grip strength with ease of component retrieval, thereby enhancing operational efficiency and reducing the risk of damage.
Tack Level Considerations
The tack level of the Gel or Vertec™ film membrane directly impacts the tray’s gripping strength. Cryspack offers a spectrum of tack levels, from ultra-low to high, allowing manufacturers to select a configuration that aligns with the handling requirements of their specific components. This flexibility enhances the tray’s usability across diverse applications and operational contexts.
Specialized Configurations
Beyond standard offerings, Cryspack provides specialized configurations of VR trays, including hinged box combinations and trays with lids. These configurations cater to unique operational needs, such as enhanced protection during transit or storage, ensuring that components remain secure and shielded from external contaminants.
Tips to Purchasing Vacuum Release Trays from Cryspack
Identifying Your Requirements
The first step in purchasing vacuum release trays is to identify your specific requirements. Consider factors such as the types and sizes of components you handle, the level of protection needed during handling and transit, and any customization preferences. Assessing these factors will help you narrow down the options and select trays that align with your operational needs and quality standards.
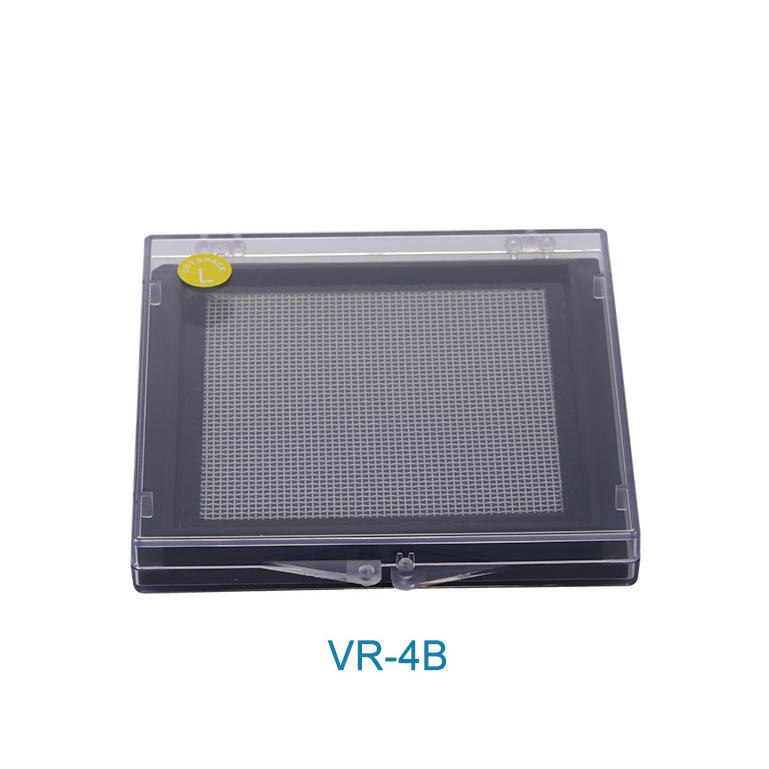
Cryspack provides a detailed Die Calculator Program that assists in determining the number of devices each tray can accommodate based on your component sizes. This tool is invaluable for optimizing tray usage and ensuring efficient production processes.
Contacting Cryspack Sales Team
To initiate your purchase, reach out to Cryspack’s dedicated sales team. You can contact them via phone at +8659187725779, email at sales@cryspack.com.cn, or WhatsApp at +86-13075917680. Communicating directly with the sales team allows you to discuss your requirements in detail, seek expert advice on tray selection, and obtain quotations tailored to your specific needs.
Cryspack’s sales representatives are knowledgeable about their product range and can provide guidance on choosing the right vacuum release trays based on your application, industry standards, and budget considerations. They can also offer information on shipping options, lead times, and any additional services or customization requests you may have.
Evaluating Product Specifications
Once you’ve connected with Cryspack’s sales team, thoroughly evaluate the product specifications provided for each vacuum release tray option. Pay attention to details such as mesh size, tack level of the film membrane, tray dimensions, and material configurations (e.g., transparent, conductive black, antistatic). Understanding these specifications ensures that the trays meet your performance expectations and compatibility requirements within your production environment.
Cryspack’s commitment to quality and customization means that they offer a range of specialized configurations, including trays with hinged lids or specialized printing options. Evaluate these features in relation to your operational needs to maximize efficiency and protection for your components.
Placing Your Order
Once you’ve chosen the vacuum release trays that best suit your requirements, proceed to place your order with Cryspack. Confirm the pricing, delivery terms, and any additional customization details discussed with the sales team. Ensure that you have all necessary documentation in place for seamless transaction processing.
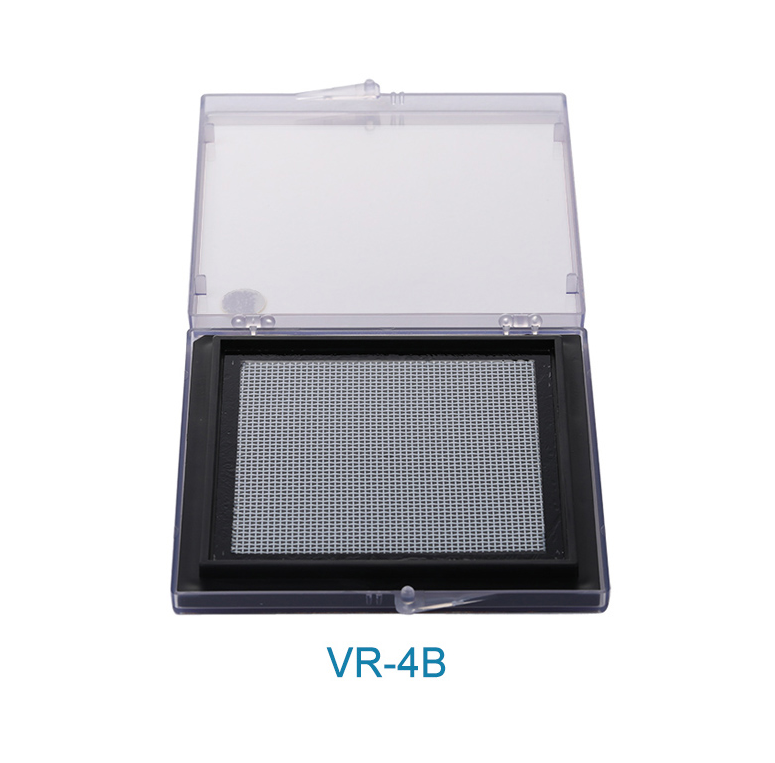
Cryspack accepts various payment methods and can accommodate specific shipping instructions to ensure your trays arrive safely and on time. They also provide ongoing customer support to address any inquiries or issues that may arise before, during, or after your purchase.
Conclusion
Cryspack’s vacuum release tray represents a pinnacle of innovation in the handling and protection of delicate electronic components. With its advanced Gel or Vertec™ film membrane technology, customizable configurations, and precise handling capabilities, the VR tray meets the rigorous demands of modern manufacturing environments. Whether in automated pick and place operations or delicate device handling, Cryspack’s VR tray stands as a testament to reliability, efficiency, and innovation in electronic component packaging solutions.